-
What happened?
A worker was bending a conical can.
During the process the worker was positioned in the area close to the can.
At that moment, the upper part of the can lost support from the machine’s upper mechanism, causing axial movement that led to a lateral slide of the plate located in the upper right area of the can.
The plate fell violently and struck the worker, causing his instant death.
-
Why did it happen?
The misalignment of the plate on the machine’s upper support was caused by axial movement that exceeded the machine’s critical stability limits.
This movement led to the plate becoming unstable and losing support.
The machine operator was responsible for repositioning the can using lateral supports to prevent axial shifts.
The worker was in a dangerous area close to the can.
-
What did they learn?
Unexpected hazards can lead to serious consequences. Organisations should regularly review processes to identify and mitigate any hidden or unforeseen risks.
Key learnings:
Improve machine safety: Re-evaluate machine designs to keep workers away from hazardous areas. Implement automated guarding systems to reduce the risk of accidents near moving or unstable machinery.
Enhance guarding and controls: Install physical barriers and interlocks to restrict access to dangerous areas. Use warning signs and sensors to stop the machine if a worker enters a restricted zone.
Conduct thorough risk assessments: Perform comprehensive risk assessments for all tasks, especially those involving unstable components. Define safe zones and enforce stopping procedures.
Provide training and raise awareness: Ensure workers are trained on machine hazards, such as instability, and the importance of staying in safe zones. Regularly update training programmes.
Implement strict supervision: Monitor high-risk operations closely with supervisors and use CCTV or alarms to detect unsafe practices.
Maintain robust inspections: Regularly inspect machines and establish maintenance schedules to ensure proper functioning of supports and safety mechanisms.
Engage with manufacturers: Collaborate with manufacturers to ensure machinery includes the latest safety features and design improvements for safer operation.
-
Ask yourself or your crew
What improvements can we make to the machines or the processes to enhance both safety and efficiency?
How can we ensure that all potential hazards, even those that seem unlikely, are properly evaluated and mitigated?
What changes can we implement internally to strengthen our risk assessments and improve hazard identification?
How can we reduce the need for workers to operate close to hazardous areas, potentially using automation or other safety controls?
What more can we do to improve the effectiveness of our training programmes and supervision to ensure safety protocols are consistently followed?
Add to homescreen
Content name
Select existing category:
Content name
New collection
Edit collection
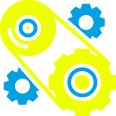
What happened?
A worker was bending a conical can.
During the process the worker was positioned in the area close to the can.
At that moment, the upper part of the can lost support from the machine’s upper mechanism, causing axial movement that led to a lateral slide of the plate located in the upper right area of the can.
The plate fell violently and struck the worker, causing his instant death.
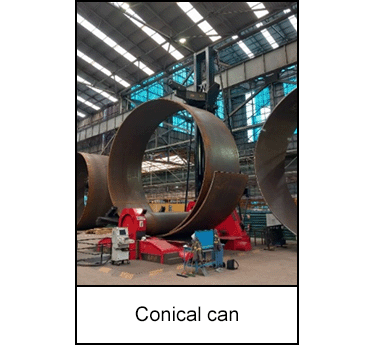
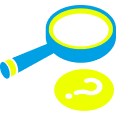
Why did it happen?
The misalignment of the plate on the machine’s upper support was caused by axial movement that exceeded the machine’s critical stability limits.
This movement led to the plate becoming unstable and losing support.
The machine operator was responsible for repositioning the can using lateral supports to prevent axial shifts.
The worker was in a dangerous area close to the can.
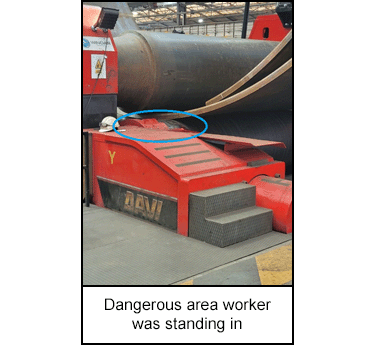
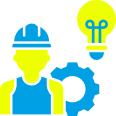
What did they learn?
Unexpected hazards can lead to serious consequences. Organisations should regularly review processes to identify and mitigate any hidden or unforeseen risks.
Key learnings:
Improve machine safety: Re-evaluate machine designs to keep workers away from hazardous areas. Implement automated guarding systems to reduce the risk of accidents near moving or unstable machinery.
Enhance guarding and controls: Install physical barriers and interlocks to restrict access to dangerous areas. Use warning signs and sensors to stop the machine if a worker enters a restricted zone.
Conduct thorough risk assessments: Perform comprehensive risk assessments for all tasks, especially those involving unstable components. Define safe zones and enforce stopping procedures.
Provide training and raise awareness: Ensure workers are trained on machine hazards, such as instability, and the importance of staying in safe zones. Regularly update training programmes.
Implement strict supervision: Monitor high-risk operations closely with supervisors and use CCTV or alarms to detect unsafe practices.
Maintain robust inspections: Regularly inspect machines and establish maintenance schedules to ensure proper functioning of supports and safety mechanisms.
Engage with manufacturers: Collaborate with manufacturers to ensure machinery includes the latest safety features and design improvements for safer operation.
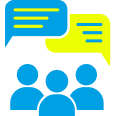
Ask yourself or your crew
What improvements can we make to the machines or the processes to enhance both safety and efficiency?
How can we ensure that all potential hazards, even those that seem unlikely, are properly evaluated and mitigated?
What changes can we implement internally to strengthen our risk assessments and improve hazard identification?
How can we reduce the need for workers to operate close to hazardous areas, potentially using automation or other safety controls?
What more can we do to improve the effectiveness of our training programmes and supervision to ensure safety protocols are consistently followed?
A worker was fatally struck by a falling plate from a conical can during a bending process, after the upper part of the can lost support from the machine and slid laterally, causing the plate to fall.